FTL公司生产管理的改进方案思考
时间:2022-10-25 来源:51mbalunwen.com
本文是一篇生产管理论文,笔者认为FTL公司的精益生产需要逐步推行,三年内可推行初见成效,五年左右可望实现全面自动化,彻底实现所有的改进方案,公司会逐步提高生产效率和产品质量,同时降低成本,五年内逐渐成为国内一流减振器公司,在竞争市场上占绝对优势。
第1章 绪论
1.1 研究背景
德国人卡尔·本茨于1885年10月研制成功世界上第一辆汽车后,人类在交通工具史上有了划时代变革,1909年美国人亨利·福特将流水生产线技术成功应用到汽车生产制造上,首次实现汽车的大批量生产,使家庭使用轿车的神话成为现实。福特的流水线生产方式的成功应用,大幅度地降低了汽车制造成本、提高了汽车生产效率、开辟了人类社会上一个庞大的汽车工业。随着时代的变迁,汽车在技术与结构上有了飞速的发展,并且朝着多样化、电子化、智能化等方向发展。同时,汽车零部件行业作为汽车的重要组成部分,也随之有了快速发展,无论从技术创新上,还是生产规模上,随着全球经济的一体化,汽车零部件产业成为汽车行业中最重要的组成部门,预计在不远的未来汽车零件部产业将占居汽车行业的核心地位,成为汽车行业的标准应用。
汽车业的发展,离不开有限的市场和有限的资源。随着人类社会的发展,人均GDP不断增高和个人购买力逐步提升,汽车需求量随之也在不断增加,仅2016年中国乘用车销售达2437.7万辆,同比增长14.87%。随着中国整车市场步入成熟期,增速将放缓,但预测2017年汽车销量仍达2525万辆,到2021年中国市场预计销售突破3000万辆。减振器作为汽车最重要的零部件之一,2017年全国预计销售将达到1亿多支,虽然市场大,但减振器的供应商也很多,竞争异常激烈。仅在中国世界知名减振器公司约有10家,如天纳克减振器、上海汇众SACHS减振器、京西重工减振器、广州昭和减振器、宁江昭和减振器、苏州东机工减振器、万都减振器、马瑞利减振器、KYB减振器、FTL减振器等,中国知名自动品牌减振器公司有100多家,具备主机厂配套资质的约有20多家减振器企业,中国庞大的配套市场,由外资和合资的减振器公司仍处于垄断地位。
1.2 研究意义
目前,在国内汽车减振器零部件制造企业的激烈竞争下,FTL公司2016年销售减振器889万支,而同等地位的竞争对手均已超过1500万支,FTL的销售利润率仅4.2%,与同等地位竞争对手相比处于低水平。而2016年市场索赔金额达到1500多万元,比2015年大幅度增长,同行业相比处于较高行列。同样,其他指标如内部废品率、管理成本等均比同行业竞争对手高。而国内减振器竞争企业众多,一流的企业为合资或独资,技术及市场较为成熟,有固定的配套生产链,其余大多为自主民营企业,虽然技术上相对落后,但成本低廉,生产效率高,也成为了强有力的竞争对手。内外部环境作用下,造就了FTL公司效益下滑,竞争力日趋低下。
而汽车市场仍在持续稳定发展,全国需求量仍在不断增长,同时减振器的需求也随之上升,预计2017年减振器需求量将达到10100万支,蛋糕虽然大,但竞争激烈,想要占有的份额多一些,其必须拥有强大的竞争力,无论从产品、服务还是成本等方面,都将是市场占有率的决定性因素。
同时,由于汽车整车企业的迅速壮大,整车制造企业竞争也变的异常激烈。目前,全国有整车制造企业约有250家之多,销售居前的有一汽大众、上汽通用、上汽大众、东风汽车、长安汽车、吉利汽车、长城汽车、一汽丰田、江淮汽车等。为了抢占市场,各整车厂都将效率、成本列为竞争的项目。努力提高自身效率,提前开发车型,抢占市场。同时大幅降低产品价格,提高销售量,最后引发价格战。成本的压力自然会降临到各零部件供应商身上,而减振器也未能幸免于难。因此,研究如何在激烈竞争中胜出将是一个企业生死存亡的课题。影响公司竞争力的关键因素在于管理的效率、成本、质量三大方面。
第2章 精益生产相关理论界定
2.1 精益生产理念与内涵
日本丰田公司最早提出了JIT的概念,即Just In Time,核心思想就是只在需要的时候生产必需量的产品,又被称作“准时化生产”。其最主要的理念是“零库存和迅速应对变化”。后来在大野耐一的带领下逐渐创造出一套具有竞争优势的生产方式,人们习惯称为“JIT”,又被称为丰田生产模式(TPS)。
丰田生产模式,即Toyota Production System,是由日本丰田汽车公司创造的,是以提高公司生命力为宗旨的一种理论、方法和工具的体系,是丰田公司生产的准则,这种体系最基本思想是“消除浪费”,采用一系列合理的生产优化,来提升产品生产的效率,并提高产品的质量,最终达到产品成本的降低。丰田生产模式首次改变了统治全球汽车工业的福特流水线生产方式,对全世界的生产制造业产生了非常深远影响。由于其合理的生产方式,使丰田一跃成为全球最大的汽车制造商之一,拯救了日本经济,故人们称其创始人大野耐一为“日本复活之父”和“生产管理教父”。
从1960年开始,以丰田为首的汽车制造企业开始推行一种新的生产模式,即TPS,并且迅速凭借其低成本、高质量的优势在汽车市场上占居领先地位,并主导了美国汽车市场,从此美日汽车贸易战拉开序幕,而此一役持续了将近10年。因为TPS追求的是最高的生产效率,消除一切浪费,美国研究学者称之为“精益生产(Lean Production)”,并逐渐开始在全世界的汽车制造业流行开来,形成了大多数汽车制造业效仿的楷模,成为全球汽车生产标准,对人类的生产革命产生了深远的影响。
2.2 精益生产系统架构
精益生产经历多次的实践、总结与完善,逐渐形成了一整套标准体系。精益生产的本质就是不断通过消除过程中的不增值活动而实现的,其目标就是既要消除浪费又要保证产品质量和产品的准时交付。在生产过程中的每个活动,都会涉及到TPS的理念,一般认为TPS由两大支柱支撑,这两大支柱分别是准时化生产和自动化,它们是精益生产的理论基石。同时从这两大支柱衍生出很多的精益生产管理思想与具体工具,可以用如图2.1所示的各个“房”进行诠释。
第一支柱是准时化生产“JIT”,意思是只在需要的时候,按需要的量,生产所需的产品。只有每个工序都能够在合适的时间收到所提供必要量的必要产品,这样才能满足准时化生产基本要求。
传统的生产方式是向每道工序都发出生产指令,采用由上道工序向下道工序推动式的生产方式,这样违背准时化生产的基本条件,因为上道工序并不清楚他的顾客——下道工序的需求,这样常常会导致多余的生产,超出所需求的数量。 所以,精益生产的做法是只向最终的工序下达生产指令,装配线涉及的所有料件都必须向上道工序来取,而上道工序也只能按下道工序需要的数量来生产,这样才有可能实现准时化生产。
实施准时化生产,可从根本上彻底解决库存在物资上和财务上为经营管理所带来的负担。实现准时化的具体工具有:拉动式生产、单件流、节拍时间、均衡生产等。
第3章 FTL公司生产管理现状分析 ............................... 19
3.1 公司生产管理现状分析 ................................... 19
3.2 公司组织机构、开发流程、生产运营现状分析 ................ 21
第4章 FTL公司生产管理改进方案的设计 ........................... 32
4.1 公司生产管理目标的确定 ..................................... 32
4.2 组织机构及精益生产团队的构建 ......................... 32
第5章 FTL公司生产方案改进评估 ............................... 50
5.1 精益生产效率提升评估 ............................... 51
5.2 精益生产质量提高评估 ................................. 52
第5章 FTL公司生产方案改进评估
5.1 精益生产效率提升评估
经过精益生产方式的推行,生产效率会有非常大的提升。对于生产效率的提升改进,改进点主要集中在组织机构重调整、工艺平衡重设计、自动化线实施、5S深入推行、全员TPM等改进上。
首先在组织机构上,经过重新计整后,部门职责进行了整合,对生产调试等过程进行了极大优化,避免了由于职能重叠或不明确造成的延误,尤其单独的项目部的成立,对整个项目的管控赋予了权力,对项目进度、成本、质量全面把握,并进行绩效考核,并采取同步开发工程,可有效缩短开发周期,将原来的八个月开发期可缩短至六个月。具体如图5.1所示。
第6章 总结与展望
6.1 总结
FTL公司的生产工艺来自日本,生产管理方式也是学习日本的管理方式,从2000年就开始投入生产,2015年又开始推行5S管理,期间在产品开发周期、生产效率、产品质量都有一定的提高,但处于竞争激烈的今天,仍不足以取得绝对优势,相对同等地位的其他竞争对手,产量及销量居中上等水平,利润率低下,人均产值处于下游水平,生产效率落后,产品质量还存在诸多问题,索赔金额大,顾客抱怨多,给进一步开拓市场带来许多困挠。本文从公司在市场上的表现入手,深入分析公司现存的问题,并剖析产生问题的根本原因,最后针对原因提出主要改进方案,并对方案评估其改进效果,总结整个分析改进过程,主要有以下几点:
(1) 精益生产推行,重在理念转换。精益生产的理论,各个企业都并不陌生,有的公司也推行数年,但效果总是欠佳。原因是只重其形不重其果,公司从老总到员工,思想仍旧是传统观念,生产框架是“精益生产模式”,却不关注推行效果与结果,不能掌握其精髓,故无论在生产效率、产品质量还是在成本并没有多大效果,值得深思。
(2) 精益生产推行离不开团队。精益生产模式涉及多个跨职能部门,需要集中各部门的智慧,共同出谋划策,制定出最优化的改进策略及方案。在执行过程中,一个部门往往孤掌难鸣,需要各个部门共同努力,完成属于自己职责范围的工作,才能完成整个改进过程。
(3) 精益生产离不开执行。精益生产模式,理论研究的再好,方案既使再优秀,若执行不下去,只能是纸上谈兵。好的执行力,离不开领导者的支持,领导者首先需要理解,能够持有公司长远发展眼光,确定规划目标,带头推行精益生产模式,才能将生产精益推行深化入、彻底化、有效化。
参考文献(略)
第1章 绪论
1.1 研究背景
德国人卡尔·本茨于1885年10月研制成功世界上第一辆汽车后,人类在交通工具史上有了划时代变革,1909年美国人亨利·福特将流水生产线技术成功应用到汽车生产制造上,首次实现汽车的大批量生产,使家庭使用轿车的神话成为现实。福特的流水线生产方式的成功应用,大幅度地降低了汽车制造成本、提高了汽车生产效率、开辟了人类社会上一个庞大的汽车工业。随着时代的变迁,汽车在技术与结构上有了飞速的发展,并且朝着多样化、电子化、智能化等方向发展。同时,汽车零部件行业作为汽车的重要组成部分,也随之有了快速发展,无论从技术创新上,还是生产规模上,随着全球经济的一体化,汽车零部件产业成为汽车行业中最重要的组成部门,预计在不远的未来汽车零件部产业将占居汽车行业的核心地位,成为汽车行业的标准应用。
汽车业的发展,离不开有限的市场和有限的资源。随着人类社会的发展,人均GDP不断增高和个人购买力逐步提升,汽车需求量随之也在不断增加,仅2016年中国乘用车销售达2437.7万辆,同比增长14.87%。随着中国整车市场步入成熟期,增速将放缓,但预测2017年汽车销量仍达2525万辆,到2021年中国市场预计销售突破3000万辆。减振器作为汽车最重要的零部件之一,2017年全国预计销售将达到1亿多支,虽然市场大,但减振器的供应商也很多,竞争异常激烈。仅在中国世界知名减振器公司约有10家,如天纳克减振器、上海汇众SACHS减振器、京西重工减振器、广州昭和减振器、宁江昭和减振器、苏州东机工减振器、万都减振器、马瑞利减振器、KYB减振器、FTL减振器等,中国知名自动品牌减振器公司有100多家,具备主机厂配套资质的约有20多家减振器企业,中国庞大的配套市场,由外资和合资的减振器公司仍处于垄断地位。
1.2 研究意义
目前,在国内汽车减振器零部件制造企业的激烈竞争下,FTL公司2016年销售减振器889万支,而同等地位的竞争对手均已超过1500万支,FTL的销售利润率仅4.2%,与同等地位竞争对手相比处于低水平。而2016年市场索赔金额达到1500多万元,比2015年大幅度增长,同行业相比处于较高行列。同样,其他指标如内部废品率、管理成本等均比同行业竞争对手高。而国内减振器竞争企业众多,一流的企业为合资或独资,技术及市场较为成熟,有固定的配套生产链,其余大多为自主民营企业,虽然技术上相对落后,但成本低廉,生产效率高,也成为了强有力的竞争对手。内外部环境作用下,造就了FTL公司效益下滑,竞争力日趋低下。
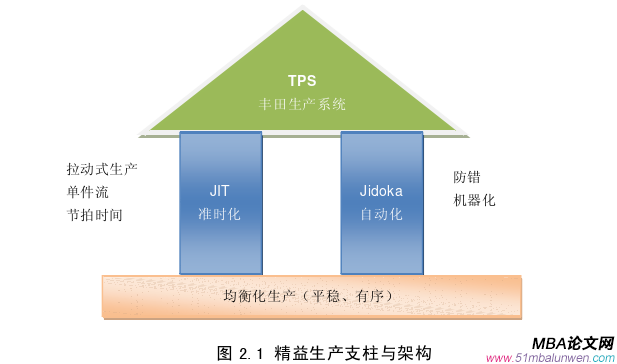
同时,由于汽车整车企业的迅速壮大,整车制造企业竞争也变的异常激烈。目前,全国有整车制造企业约有250家之多,销售居前的有一汽大众、上汽通用、上汽大众、东风汽车、长安汽车、吉利汽车、长城汽车、一汽丰田、江淮汽车等。为了抢占市场,各整车厂都将效率、成本列为竞争的项目。努力提高自身效率,提前开发车型,抢占市场。同时大幅降低产品价格,提高销售量,最后引发价格战。成本的压力自然会降临到各零部件供应商身上,而减振器也未能幸免于难。因此,研究如何在激烈竞争中胜出将是一个企业生死存亡的课题。影响公司竞争力的关键因素在于管理的效率、成本、质量三大方面。
第2章 精益生产相关理论界定
2.1 精益生产理念与内涵
日本丰田公司最早提出了JIT的概念,即Just In Time,核心思想就是只在需要的时候生产必需量的产品,又被称作“准时化生产”。其最主要的理念是“零库存和迅速应对变化”。后来在大野耐一的带领下逐渐创造出一套具有竞争优势的生产方式,人们习惯称为“JIT”,又被称为丰田生产模式(TPS)。
丰田生产模式,即Toyota Production System,是由日本丰田汽车公司创造的,是以提高公司生命力为宗旨的一种理论、方法和工具的体系,是丰田公司生产的准则,这种体系最基本思想是“消除浪费”,采用一系列合理的生产优化,来提升产品生产的效率,并提高产品的质量,最终达到产品成本的降低。丰田生产模式首次改变了统治全球汽车工业的福特流水线生产方式,对全世界的生产制造业产生了非常深远影响。由于其合理的生产方式,使丰田一跃成为全球最大的汽车制造商之一,拯救了日本经济,故人们称其创始人大野耐一为“日本复活之父”和“生产管理教父”。
从1960年开始,以丰田为首的汽车制造企业开始推行一种新的生产模式,即TPS,并且迅速凭借其低成本、高质量的优势在汽车市场上占居领先地位,并主导了美国汽车市场,从此美日汽车贸易战拉开序幕,而此一役持续了将近10年。因为TPS追求的是最高的生产效率,消除一切浪费,美国研究学者称之为“精益生产(Lean Production)”,并逐渐开始在全世界的汽车制造业流行开来,形成了大多数汽车制造业效仿的楷模,成为全球汽车生产标准,对人类的生产革命产生了深远的影响。
2.2 精益生产系统架构
精益生产经历多次的实践、总结与完善,逐渐形成了一整套标准体系。精益生产的本质就是不断通过消除过程中的不增值活动而实现的,其目标就是既要消除浪费又要保证产品质量和产品的准时交付。在生产过程中的每个活动,都会涉及到TPS的理念,一般认为TPS由两大支柱支撑,这两大支柱分别是准时化生产和自动化,它们是精益生产的理论基石。同时从这两大支柱衍生出很多的精益生产管理思想与具体工具,可以用如图2.1所示的各个“房”进行诠释。
第一支柱是准时化生产“JIT”,意思是只在需要的时候,按需要的量,生产所需的产品。只有每个工序都能够在合适的时间收到所提供必要量的必要产品,这样才能满足准时化生产基本要求。
传统的生产方式是向每道工序都发出生产指令,采用由上道工序向下道工序推动式的生产方式,这样违背准时化生产的基本条件,因为上道工序并不清楚他的顾客——下道工序的需求,这样常常会导致多余的生产,超出所需求的数量。 所以,精益生产的做法是只向最终的工序下达生产指令,装配线涉及的所有料件都必须向上道工序来取,而上道工序也只能按下道工序需要的数量来生产,这样才有可能实现准时化生产。
实施准时化生产,可从根本上彻底解决库存在物资上和财务上为经营管理所带来的负担。实现准时化的具体工具有:拉动式生产、单件流、节拍时间、均衡生产等。
第3章 FTL公司生产管理现状分析 ............................... 19
3.1 公司生产管理现状分析 ................................... 19
3.2 公司组织机构、开发流程、生产运营现状分析 ................ 21
第4章 FTL公司生产管理改进方案的设计 ........................... 32
4.1 公司生产管理目标的确定 ..................................... 32
4.2 组织机构及精益生产团队的构建 ......................... 32
第5章 FTL公司生产方案改进评估 ............................... 50
5.1 精益生产效率提升评估 ............................... 51
5.2 精益生产质量提高评估 ................................. 52
第5章 FTL公司生产方案改进评估
5.1 精益生产效率提升评估
经过精益生产方式的推行,生产效率会有非常大的提升。对于生产效率的提升改进,改进点主要集中在组织机构重调整、工艺平衡重设计、自动化线实施、5S深入推行、全员TPM等改进上。
首先在组织机构上,经过重新计整后,部门职责进行了整合,对生产调试等过程进行了极大优化,避免了由于职能重叠或不明确造成的延误,尤其单独的项目部的成立,对整个项目的管控赋予了权力,对项目进度、成本、质量全面把握,并进行绩效考核,并采取同步开发工程,可有效缩短开发周期,将原来的八个月开发期可缩短至六个月。具体如图5.1所示。
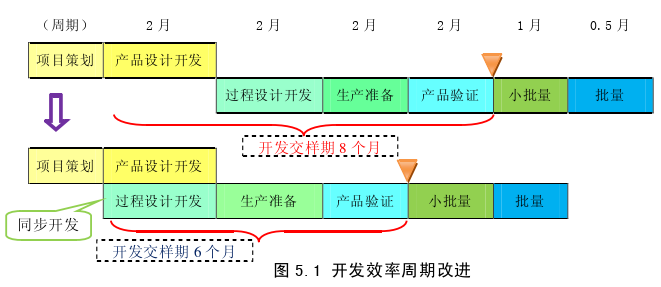
6.1 总结
FTL公司的生产工艺来自日本,生产管理方式也是学习日本的管理方式,从2000年就开始投入生产,2015年又开始推行5S管理,期间在产品开发周期、生产效率、产品质量都有一定的提高,但处于竞争激烈的今天,仍不足以取得绝对优势,相对同等地位的其他竞争对手,产量及销量居中上等水平,利润率低下,人均产值处于下游水平,生产效率落后,产品质量还存在诸多问题,索赔金额大,顾客抱怨多,给进一步开拓市场带来许多困挠。本文从公司在市场上的表现入手,深入分析公司现存的问题,并剖析产生问题的根本原因,最后针对原因提出主要改进方案,并对方案评估其改进效果,总结整个分析改进过程,主要有以下几点:
(1) 精益生产推行,重在理念转换。精益生产的理论,各个企业都并不陌生,有的公司也推行数年,但效果总是欠佳。原因是只重其形不重其果,公司从老总到员工,思想仍旧是传统观念,生产框架是“精益生产模式”,却不关注推行效果与结果,不能掌握其精髓,故无论在生产效率、产品质量还是在成本并没有多大效果,值得深思。
(2) 精益生产推行离不开团队。精益生产模式涉及多个跨职能部门,需要集中各部门的智慧,共同出谋划策,制定出最优化的改进策略及方案。在执行过程中,一个部门往往孤掌难鸣,需要各个部门共同努力,完成属于自己职责范围的工作,才能完成整个改进过程。
(3) 精益生产离不开执行。精益生产模式,理论研究的再好,方案既使再优秀,若执行不下去,只能是纸上谈兵。好的执行力,离不开领导者的支持,领导者首先需要理解,能够持有公司长远发展眼光,确定规划目标,带头推行精益生产模式,才能将生产精益推行深化入、彻底化、有效化。
参考文献(略)
相关阅读
- 供电作业项目安全生产风险管控系统开发及后评价研究2018-01-28
- 6S生产管理在浙江农行的应用与提升研究2018-02-01
- LY市甲醛行业安全生产多元化管理研究2018-02-13
- L公司中层生产管理人员薪酬体系优化研究2018-03-07
- DL植物工厂规模化经营生产战略管理研究2018-03-23
- 美卓矿机机械加工件的逆向定价生产管理研究2018-04-23
- 核电数字化分布式仪控系统研制进度风险管理研究2018-05-02
- 尾砂坝加高工程和加高后安全生产管理措施的研究2018-05-15
- 武汉铁路局漯河车站行车安全生产管理分析研究2018-05-18
- 轨道交通供电运行安全生产管理系统研究与应用2018-05-31